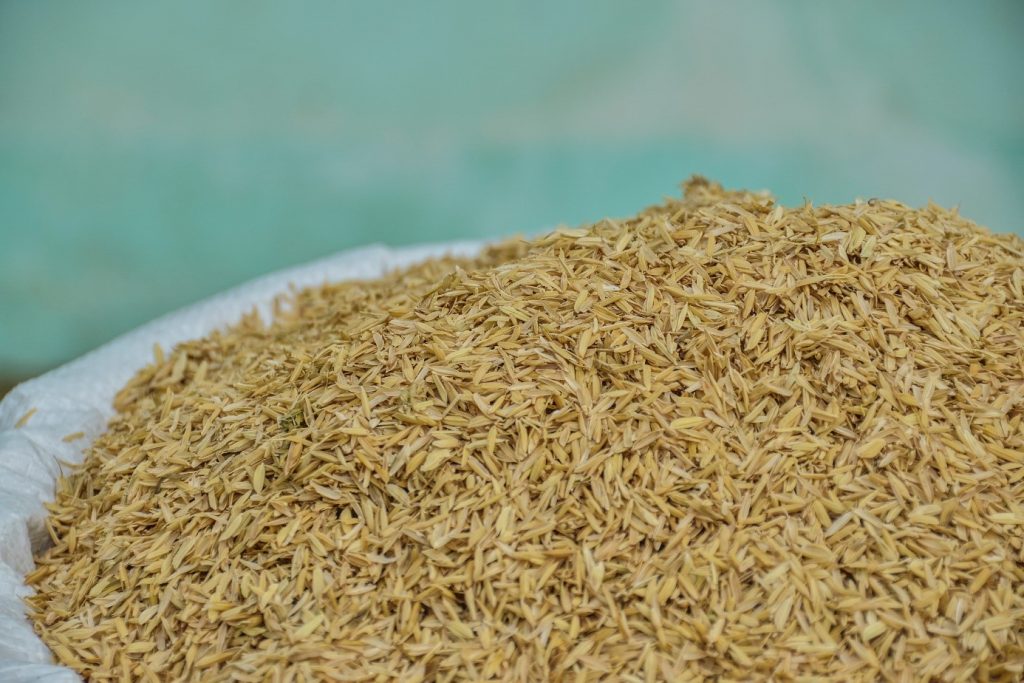
The afternoon heat is unusually bearable as Dr. Ricardo Orge and I walk through a path that leads to a portion of the farm. The road divides the sprawling rice field to the left and irrigation canal to the right.
As we reach the site, we went straight to the oven housed in a shed.
“This is where they pasteurize the mushroom fruiting bags,” Dr. Orge reveals.
But the oven is not what we came here for. Behind it, a pipe is attached that goes through the wall where another machine is connected.
“That’s where the heat comes from,” Dr. Orge points.
He then leads me to the back of the wall where the pipe is connected to the conical-shaped tank made of black iron sheet. I grab the chair near me and stood on top of it.
“Do you see it?” Dr. Orge asks as he placed his flashlight inside the tank.
I peek and the burnt smell festered my nostrils; there lies a sight of yellow and black hues of rice hull sitting at the bottom. Suddenly, it all came to me. This is no ordinary chimney.
Dr. Orge leans to open the two front tubes of the chimney. The upper tube regulates the air that comes in and out of the chimney and the lower one is where the burnt rice hull comes out.
The machine that Dr. Orge developed is not exactly what it looks like today since he first designed it 2010, back when he was taking his PhD on energy engineering at the University of the Philippines Diliman. It had undergone minor tweaking to perfect the partial burning or carbonization process, making sure that the machine would regulate enough heat to carbonize the rice hull.
Dr. Orge, the 58-year old government-conferred scientist based at the Philippine Rice Research Institute (PhilRice), is one of the many engineers in the world, from Europe to Asia, who are transforming rice hull into an alternative source of energy.
“Rice hull is no longer the waste or unwanted agricultural by-product that it used to be,” says Dr. Orge. He cites how a few years ago, he could only ask it from millers for free when he was still developing the device.
Today, every 60 sacks cost more or less P1,200 or $23.
From waste to energy
The rice hull or husk is the outer layer that covers the rice grain. During milling, the hull is detached from the grain, producing 20% of “waste.” For farmers and millers who have limited knowledge on how to properly manage it, the hull is one of those agricultural by-products often disposed on the roadside or burnt on the field.
Dr. Orge is one of the biomass experts in the world who saw rice hull’s massive potential in renewable energy. Rightfully so, as rice is a major staple food consumed by more than half of the world’s population. Data from International Rice Research Institute (IRRI) showed that in 2018, the world produced more than 700 million tons of rice. But when we talk about rice production, Asia is on the forefront, where it contributes to 90% of the global rice production.
“With the rising fuel prices, effects of climate change, and ballooning population, it has become even more challenging and expensive for us to produce rice,” Dr. Orge shares.
If the hull constitutes 20% of the total weight of the grain, seeing how much residues are produced annually, then it is understandable why engineers around the globe like Dr. Orge are developing machines to convert rice hull into renewable and sustainable energy – performing various processes such as pyrolysis, gasification, and carbonization.
‘Under pressure’
At PhilRice alone, engineers have developed a gasifier that uses rice hull to power water pumps on the field for irrigation. They have also developed a rice hull stove that conducts perfect combustion for cooking. A few kilometers away from PhilRice, an energy corporation was established that uses the by-product to generate electricity.
Meanwhile, Dr. Orge focuses on carbonization, a process that converts rice hull into biochar or charcoal that is used as soil amendment in rice production. Before he planned how the machine was going to look like, he scoured the literature and studied various designs of rice hull carbonizers.
“Most of them were conventional ‘open-type’ carbonizers and the setback of using these is that the generated heat from carbonization goes into the air,” Orge explains.
In other words, heat or energy, is wasted.
Dr. Orge wanted to improve the open-type carbonizer and design a prototype with a heat recovery system.
With series of test runs and published papers in journals, Dr. Orge also partnered with PhilRice engineer John Eric Abon for the design refinements of the machine. And finally, in 2013, the two came up with a prototype now called the Continuous-type Rice Hull (CtRH) Carbonizer that requires 20kg of rice hull per hour and produces two products: biochar and heat.
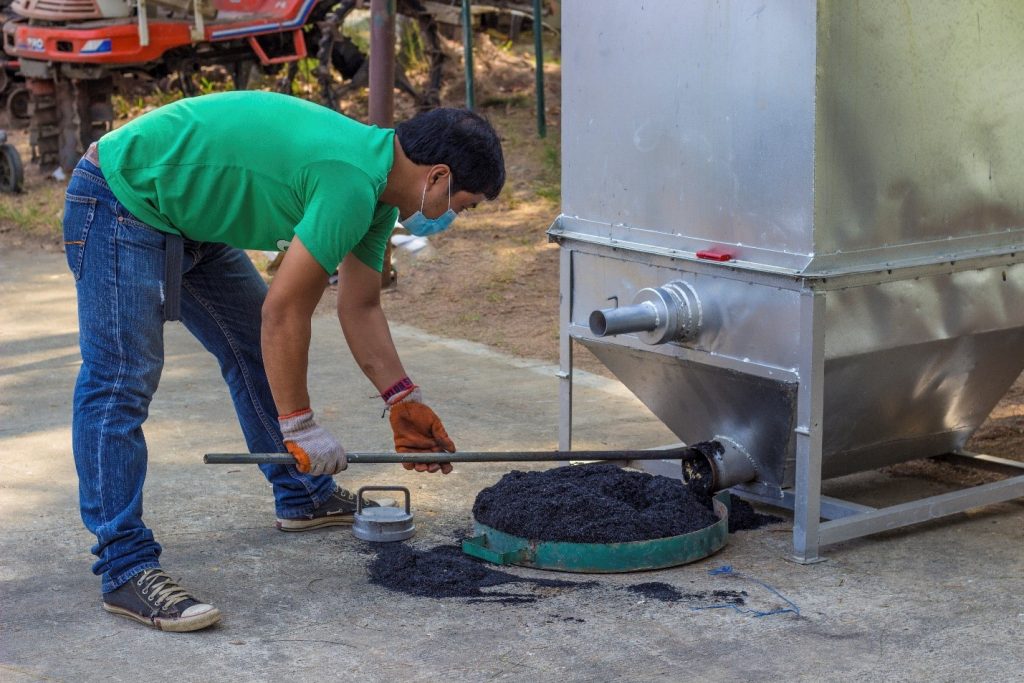
One-two punch
What makes biochar and heat from CtRH Carbonizer important?
For Dr. Orge, the two products could help sustain the livelihood of small-scale rice farmers living in the Philippines, often cited as one of the most-vulnerable countries to climate change.
The International Biochar Initiative, on its website, explains that large amounts of agricultural biomass are burned or left to decompose, releasing carbon dioxide and methane into the atmosphere. Using agricultural wastes to make biochar removes them in the pollution cycle.
The carbonized rice hull, according to PhilRice, contains micronutrients such as phosphorous (P), potassium (K), calcium (Ca), magnesium (Mg), that are vital for growing crops. In rice production, farmers can use it as soil conditioner, organic fertilizer, waste water filter, and pest control agent.
Heat generated from the CtRH carbonizer, on the other hand, is used to the cooking attachment for pasteurizing mushroom fruiting bags (MFBs). The mushroom production is an income-generating activity in the integrated rice-based farming system PhilRice calls as Palayamanan.
Dr. Orge and his co-authors in their published paper found that the system they developed could eliminate wood as fuel in the steam pasteurization of MFBs.
“The heat generated by the CtRH carbonizer, which was determined to be 1,083.6 MJ for the 8-h operating time, was sufficient to provide the energy requirement of pasteurizing 533 MFBs,” wrote the authors.
This way, farmers will no longer be encouraged to cut trees to make firewood to be used for cooking or as fuel for steams.
Scientist for the farmers
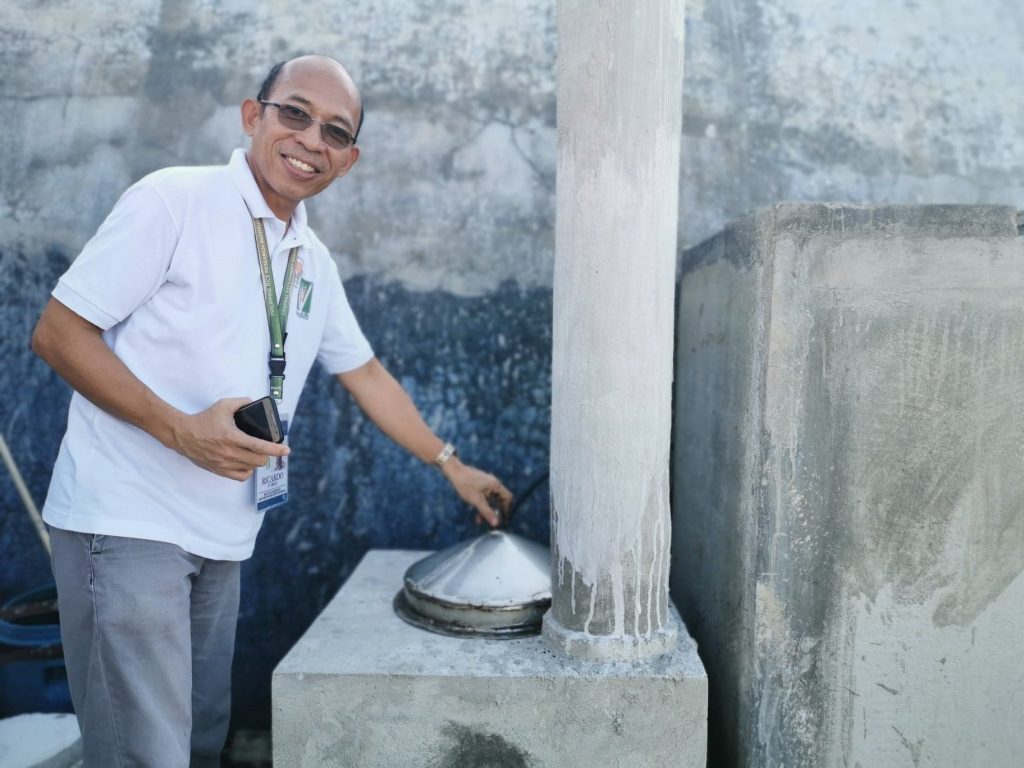
In 2017, Dr. Orge was the lone awardee of the Manila Water Foundation Prize for Engineering Excellence for inventing the CtRH Carbonizer.
It is continuously used by farmers in Palayamanan communities in the provinces of Nueva Ecija and Pangasinan.
Dr. Orge and his team are now studying how to liquify the heat generated by the carbonizer to be used as fuel for machines particularly for land preparation.
“While the carbonizer is a tool for farmers to help mitigate the effects of climate change, I plan to conduct research on a more sustainable system to address farmers’ use of fossil fuel,” he says with certainty.
But the scientist will continue to promote the use of biochar, a product that will never go away in the new system he plans to develop.
“I believe that what we get from the soil must go back to the soil,” the scientist concludes.